Small Footprint, Big Results.
A Multitasking Machine That Transforms Your Shop Floor
NT-Flex
Compact Meets Flexibility
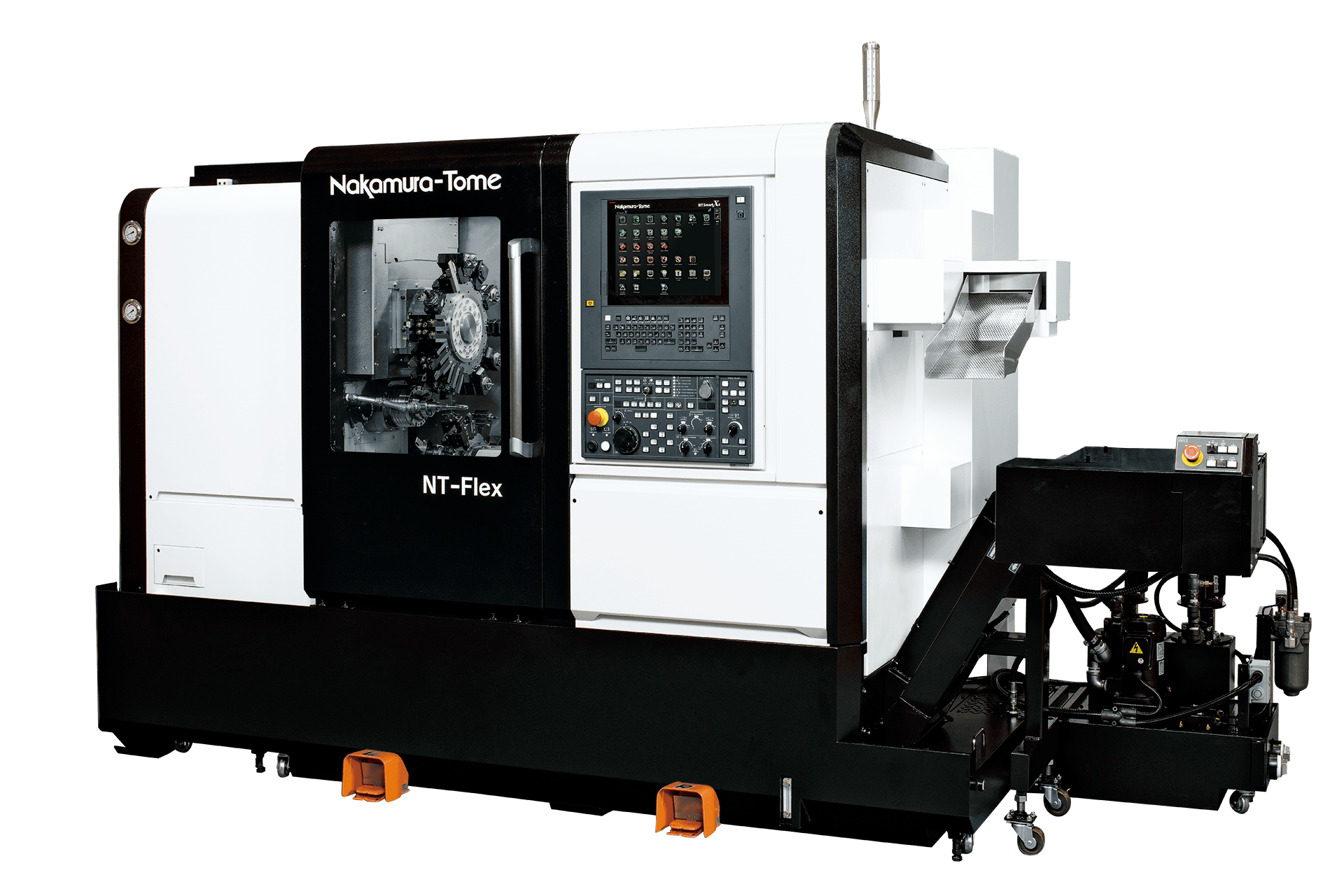
Is Your Shop Floor Facing Efficiency Challenges?
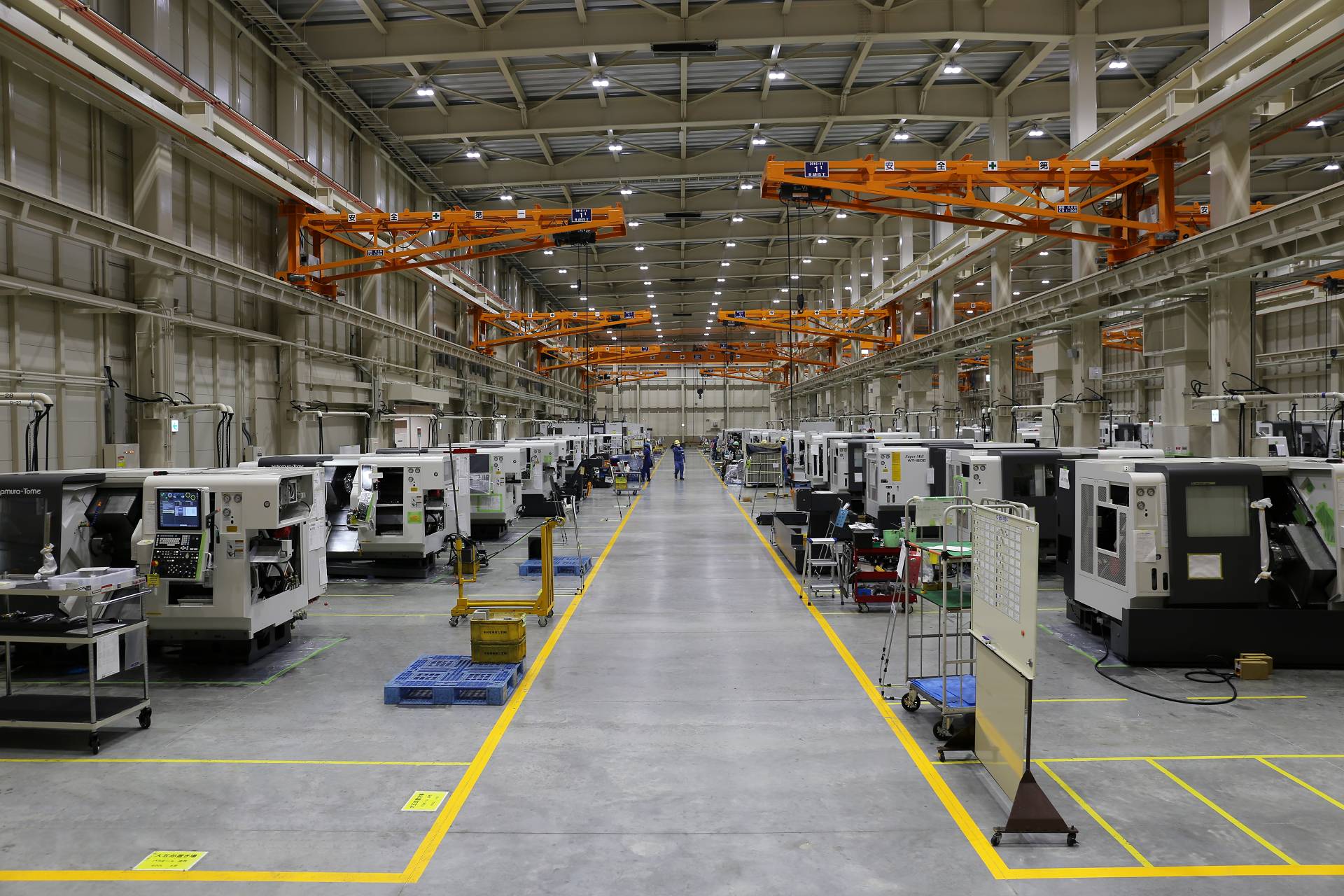
Limited space makes it difficult to install new machines or rearrange your factory layout, but you still need to boost productivity.
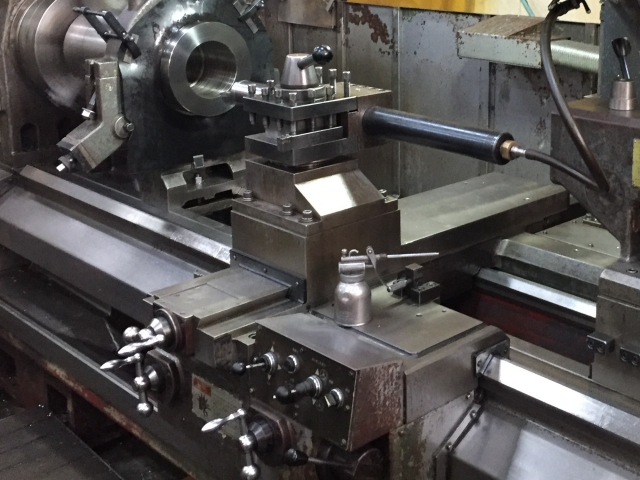
Frequent changeovers are needed, but setup takes too much time.
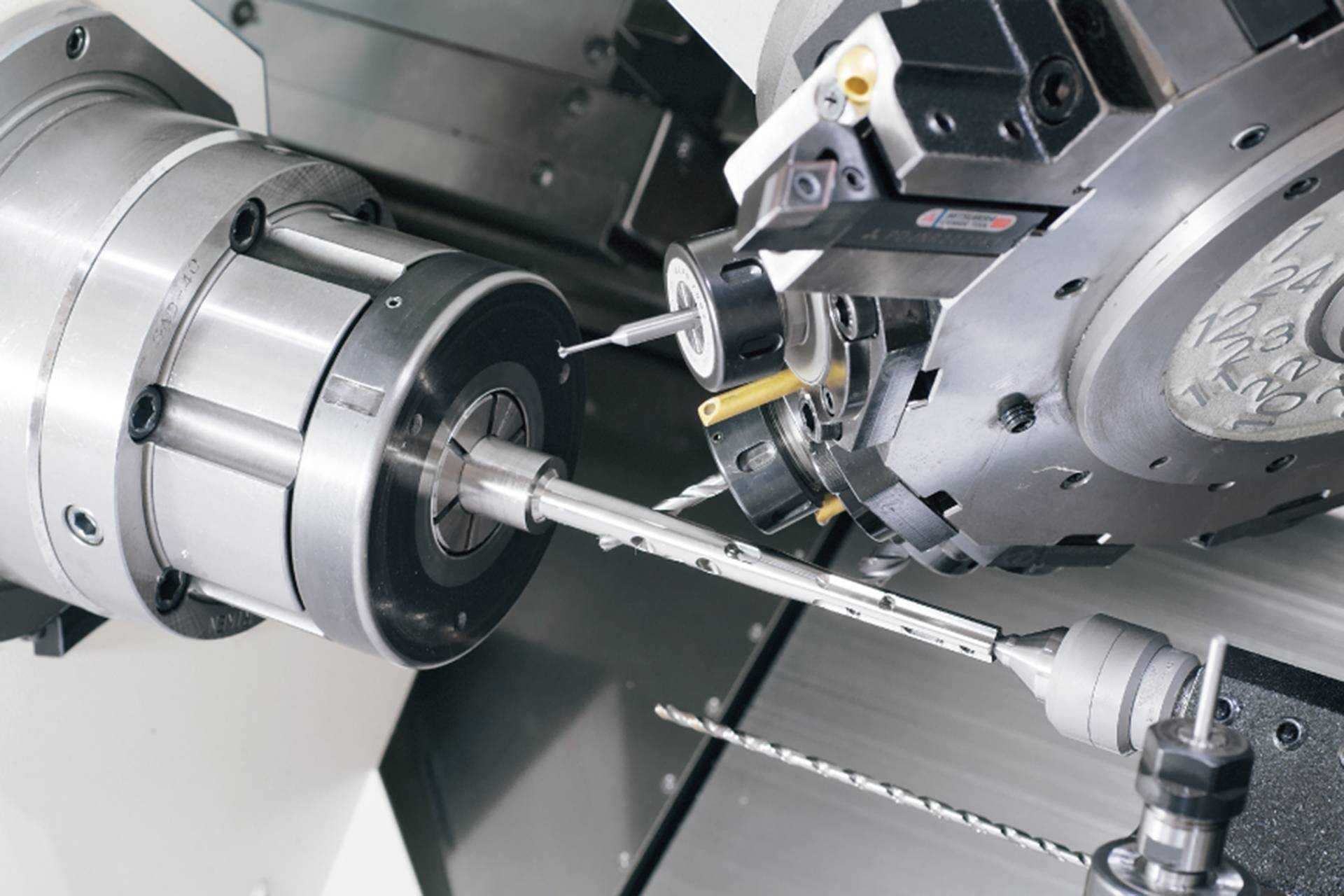
Parts are becoming smaller and more difficult, but your machines can’t finish them completely.
NT-Flex solves these challenges, maximizes your factory’s productivity, and helps you respond to diverse customer needs with confidence.
NT-Flex Benefits
With a footprint of just 1.38 meters in depthー This compact machine completes all processes in one setup.
NT-Flex is a precision multitasking CNC lathe with 2 spindles and 2 turrets, designed to maximize the use of limited factory floor space without any wasted gaps. Featuring a standard milling function and Y-axis on the upper turret, this compact machine can efficiently handle machining for over 100 different product types, helping your production meet diverse customer demands.
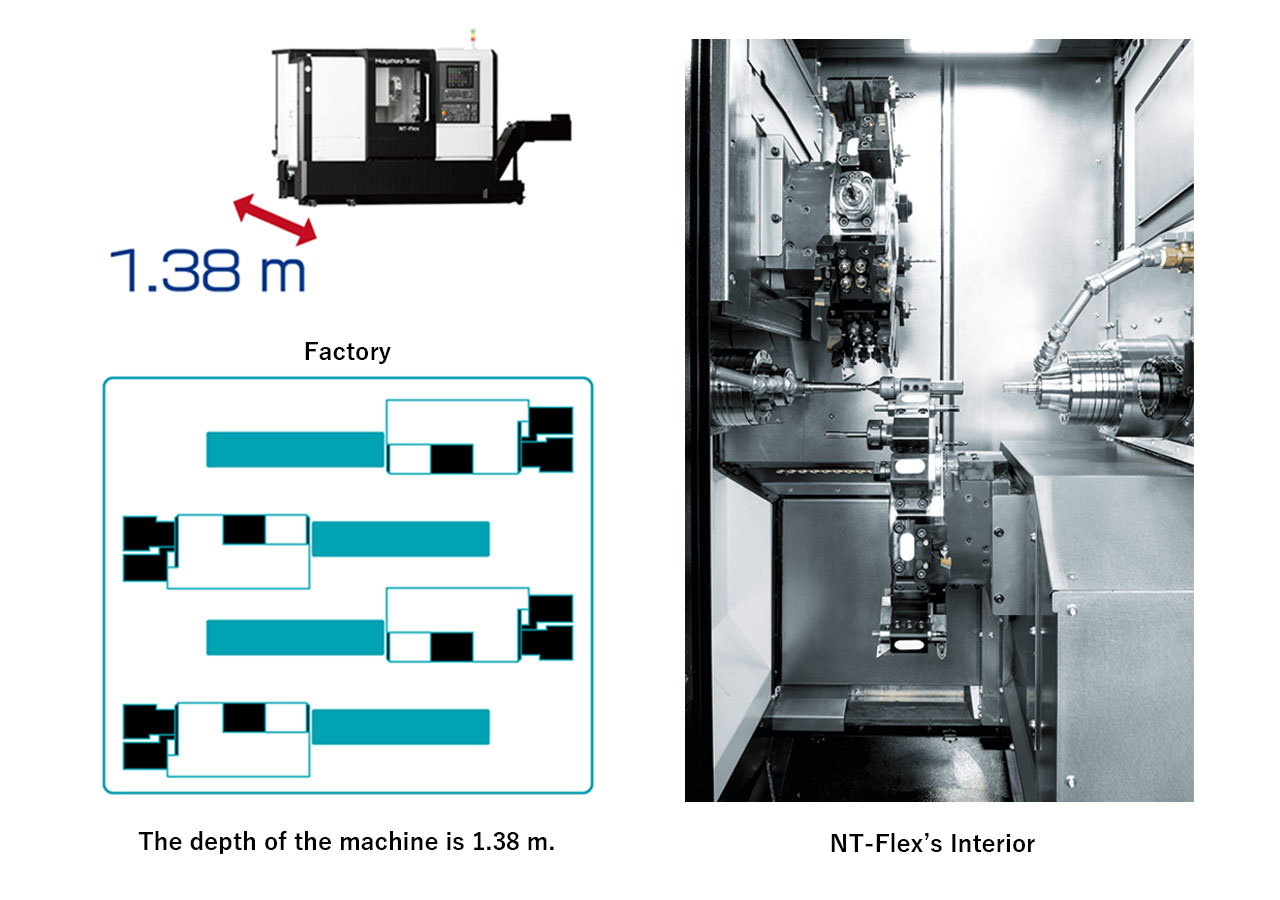
Equipped with up to 96 tools! NT-Flex meets the diverse needs of increasingly complex workpieces.
Despite its compact size, it features two 24-station turrets—one upper and one lower. By using quadruple holders, it can accommodate up to 96 tools. This single machine handles all machining processes, including turning, milling, and gear cutting.
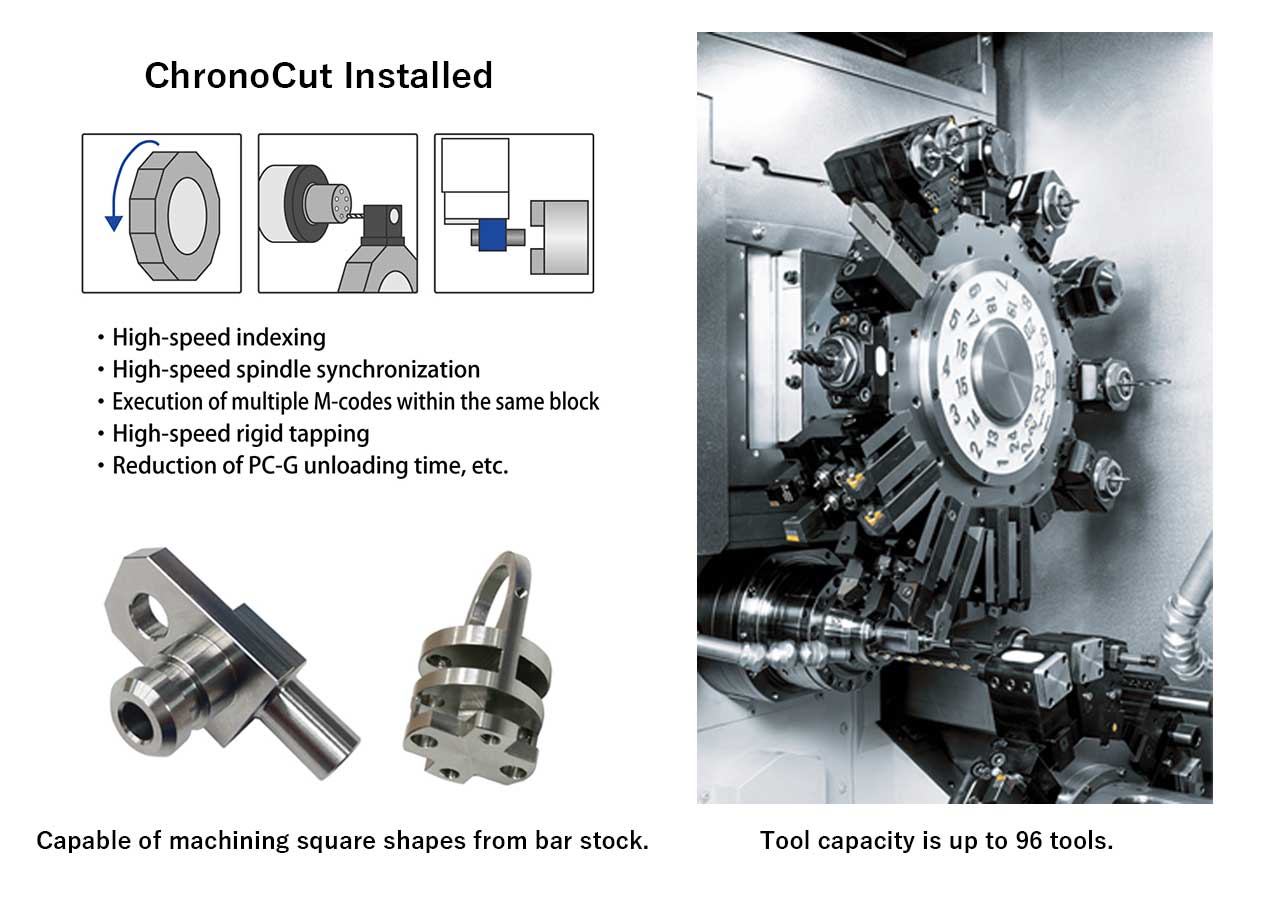
Combining multiple processes boosts efficiency and cuts costs.
A multitasking machine enables process integration, allowing multiple machining steps to be done on a single machine instead of separate lathes or machining centers. This reduces inventory and labor costs, saves space, and streamlines production.
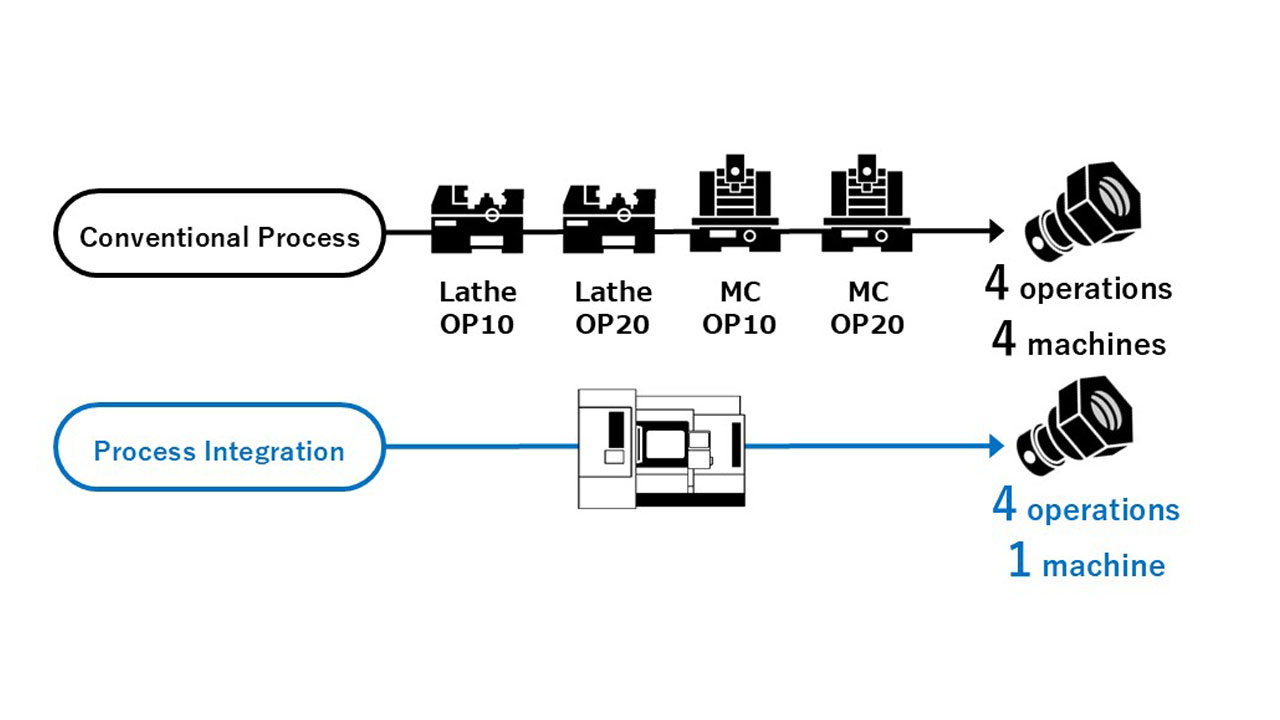
Specifications
φ32mm | φ38mm(op.) | |
---|---|---|
Max. Turning Diameter | φ150mm | φ150mm |
Max. Turning Length | 250mm | 250mm |
Distance Between Spindles | max.655mm/min.200mm | max.655mm/min.200mm |
Bar Capacity | 32mm | 38mm |
Chuck Size | 5″ | 5″ |
L/R Spindle Speed | 8,000min-1 | 8,000min-1 |
L/R Spindle Drive Motor | 7.5/5.5kW | 7.5/5.5kW |
Floor space | height:2,010mm/width:3,500mm/depth:1,380mm | height:2,010mm/width:3,500mm/depth:1,380mm |
NT-Flex is equipped with Oscillation Cutting(*) as standard to improve chip evacuation and offers the optional Triangle Cut feature for enhanced chip control.
*Oscillating Cutting is available on the Z-axis only.
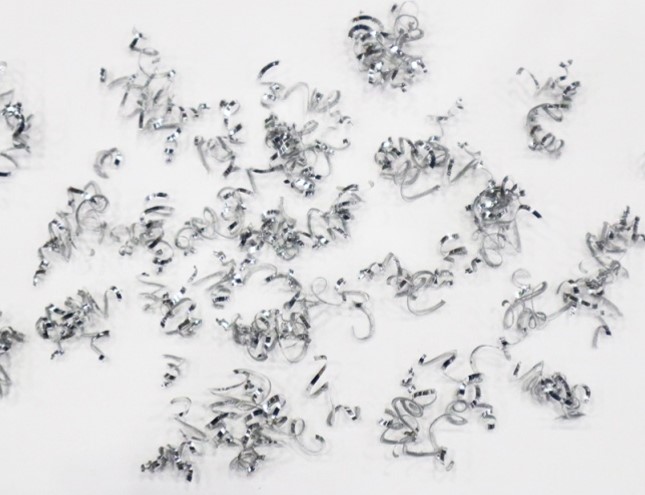
Oscillating Cutting
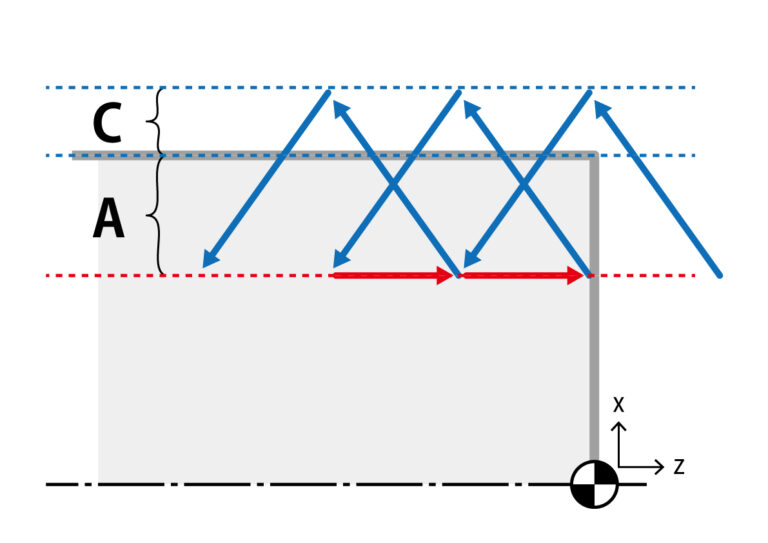
Triangle Cut
Related Videos
-
[New] NT-Flex | Compact Meets Flexibility
-
Produce 100 Types of Parts with a Compact 1.38m Depth Machine: NT-Flex!
-
Semiconductor Parts Machining with Compact 1.38m Multitasking Machine 「NT-Flex」
-
EV Motor Shaft Parts Machining with Compact 1.38m Multitasking Machine 「NT-Flex」
Frequently Asked Questions
-
What are the benefits of introducing a multitasking machine?
By introducing a multitasking machine, multiple processes can be completed on a single machine. This eliminates the need for setup changes and workpiece transfers between different machines, significantly improving overall operational efficiency. Since the entire process is completed in one cycle, machining accuracy remains consistent, leading to higher product quality. Moreover, with fewer machines required, your factory layout can be optimized, making better use of available floor space. In short, multitasking machines help streamline production, enhance precision, and optimize resource allocation, resulting in more efficient and flexible manufacturing.
-
What types of components are best suited for multitasking machines?
Multitasking machines are especially suitable for complex-shaped parts and shaft-type components. Because they can perform both turning and milling in a single setup, they are ideal for producing high-precision parts. They are also well-suited for small-lot production where frequent product changeovers are required. Thanks to simplified setup processes, multitasking machines offer great flexibility and productivity in high-mix, low-volume manufacturing environments.
-
What preparations are needed before introducing a multitasking machine?
The first step in introducing a multitasking machine is to clearly define the size, shape, and material of the parts to be machined. Next, it is important to prepare the installation environment, including checking the available floor space, power supply, and floor load capacity. It is also essential to plan training in advance so that operators can learn how to use the machine and acquire the necessary programming skills. Additionally, considering the introduction and effective use of CAD/CAM software will help streamline the creation of machining programs and enhance overall productivity.
-
Are the machine operation and maintenance difficult?
Operating and maintaining a multitasking machine requires some initial training, but rest assured — the experienced staff of our authorized distributors will provide thorough guidance during installation to ensure a smooth start.
Start by downloading our free product catalog.
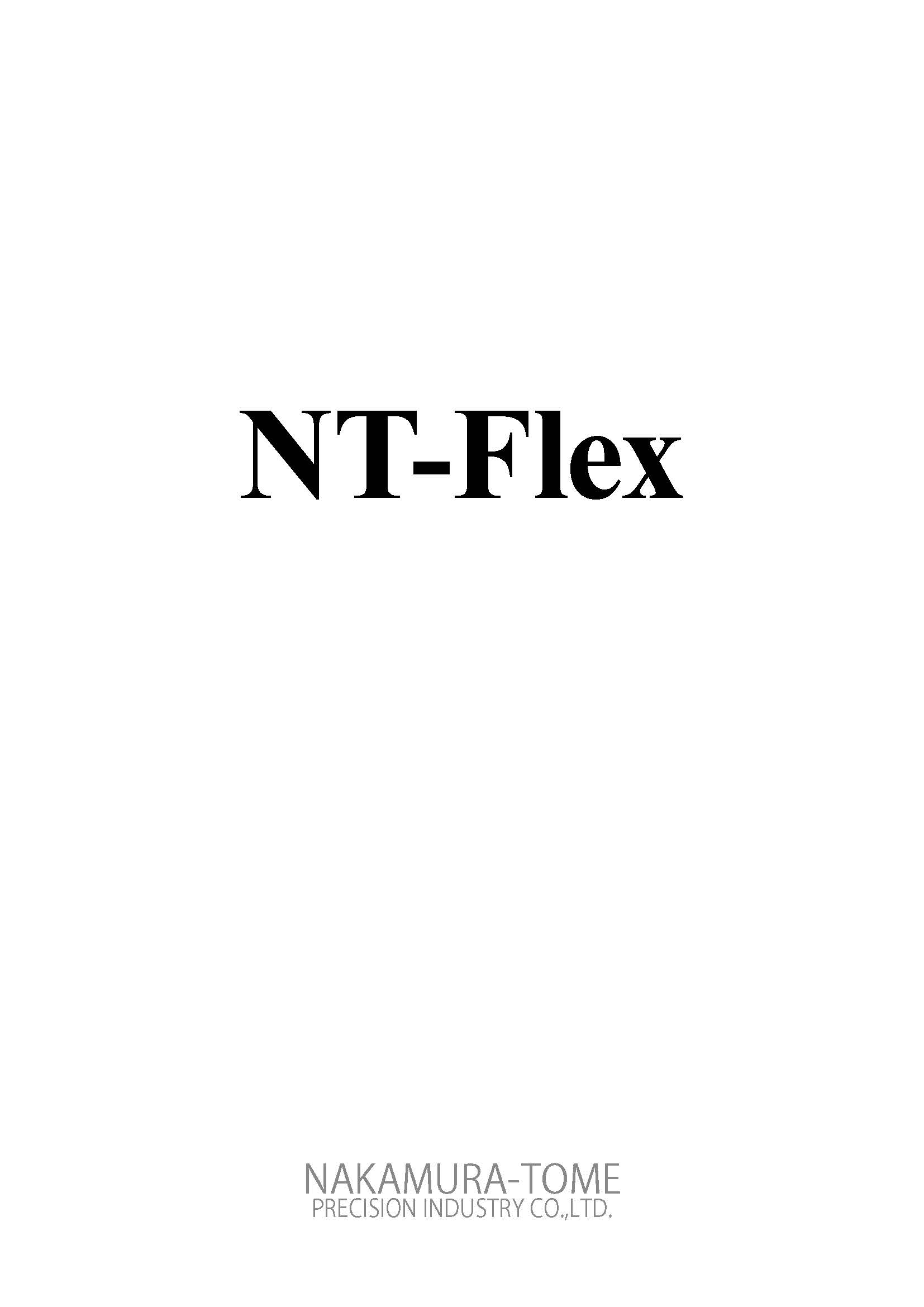
Recommended for:
- Manufacturers in urban areas or small to mid-sized factories, where floor space is always a limiting factor.
- Those handling more custom orders or made-to-order production and need greater flexibility in operations.
- Companies experiencing missed opportunities due to sudden orders or design changes they can’t respond to quickly enough.