1.What Is Gear Machining?
Gear machining refers to the process of shaping gears that transmit, adjust, or convert power. Gears come in many types depending on their function, and each requires a specific machining method.
If you’re new to gears and want to learn more before diving into machining methods, check out the related article as follows.
Related Article
Types of Gears Explained: What Do Their Shapes Mean?
A gear is a circular or cylindrical component with teeth along its outer edge. Gears work by meshing together to transmit, modify, or adjust power from motors or other driving forces.
2. Gear Machining: Then and Now
Traditionally, gear machining required multiple separate processes—turning, milling, and hobbing—each performed on a dedicated machine. Whenever the gear shape changed, different hobbing machines and cutters were needed. This meant frequent setup changes and increased workload for operators. If the gear needed to be aligned with another shape, additional phase adjustment was also required, ultimately reducing production efficiency.
Today, multitasking machines allow you to complete various types of gear machining on a single machine—streamlining the process and boosting productivity.
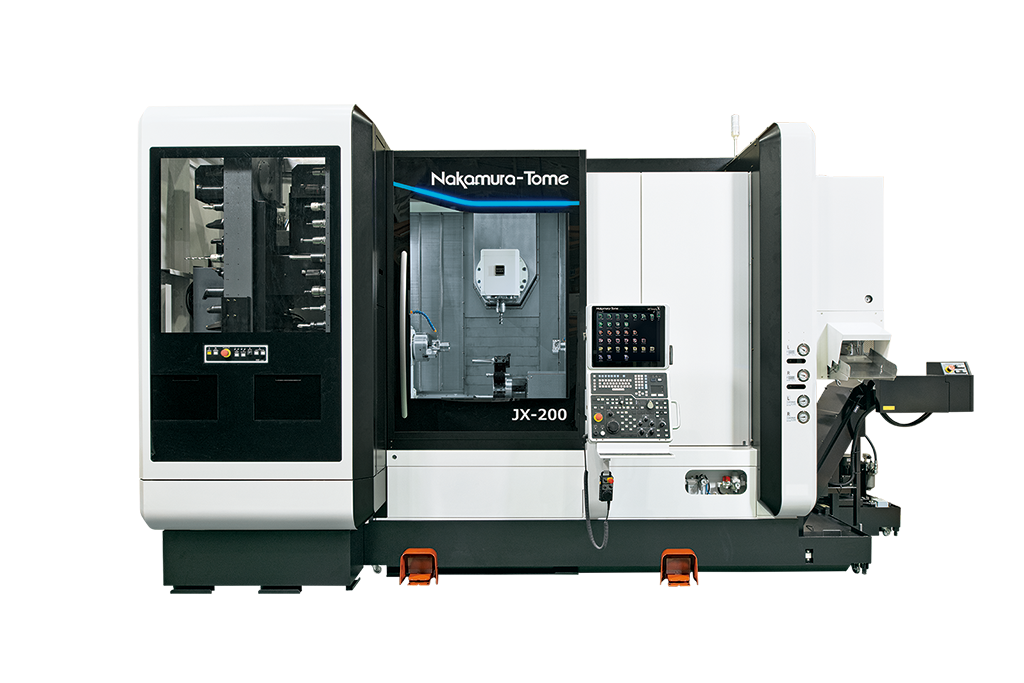
3. Gear Machining Methods and How to Choose Them
Gear machining typically falls into two main categories: generating methods and forming methods. In this article, we’ll focus on how these methods can be applied using a multitasking machine.
With a multi-tasking machine, you can simply choose the machining method that best suits your parts, and produce the gear in a single setup.
Common generating methods include hobbing and gear skiving, while forming methods involve techniques like gear shaping, gear milling, and standard milling. Let’s take a closer look at the features of each.
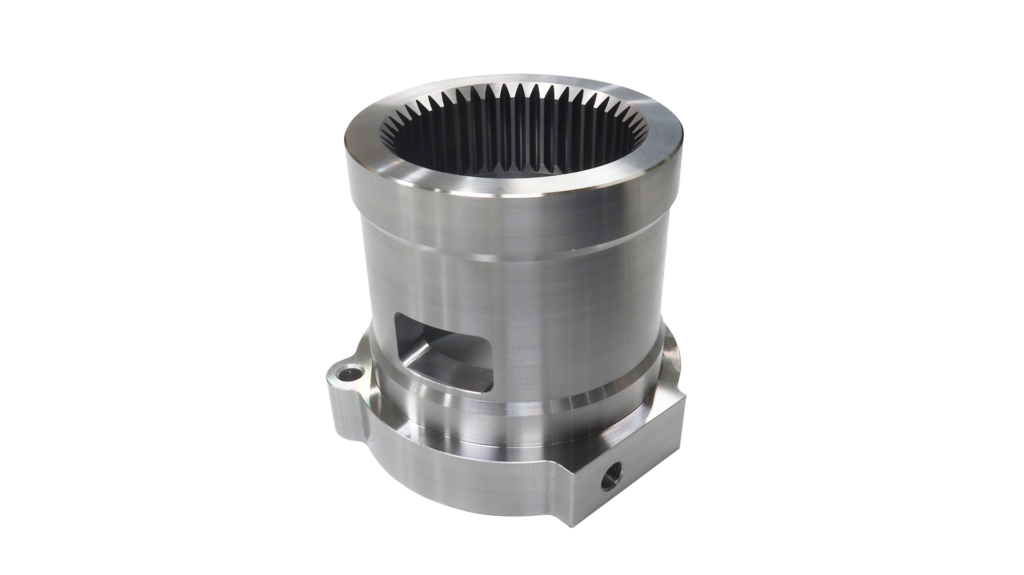
3-1. Hobbing
Hobbing is a gear cutting method that uses a specialized tool called a hob cutter. On a multitasking machine equipped with an automatic tool changer (ATC), tool changes can be performed automatically if the necessary tools are preloaded in the magazine. By setting multiple hob cutters in advance, various types of gears can be machined on a single machine.
For turret-type multitasking lathes, gear cutting is also possible using a hob holder. Mounting multiple dedicated holders on the turret enables automated tool changes—just like on ATC-equipped machines.
Either way, gear machining can be done on a single machine, improving overall productivity.
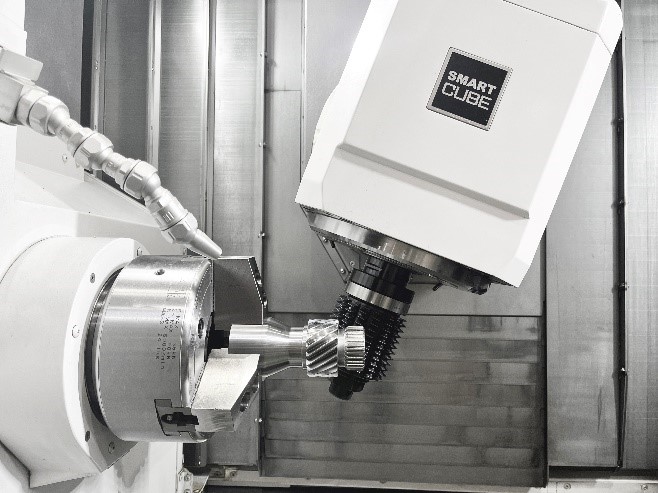
3-2. Gear Skiving
Gear skiving is a machining process where the skiving cutter and the workpiece are positioned at a specific crossing angle. This method is particularly effective for cutting internal gears, which cannot be handled by hobbing. Skiving is also advantageous when machining areas with steps or interfering features near the gear, allowing the cutter to approach and machine otherwise inaccessible areas.
Unlike some methods, gear skiving is not confined to multitasking machines with an ATC. With a dedicated skiving holder, it can also be performed on turret-type multitasking lathes.
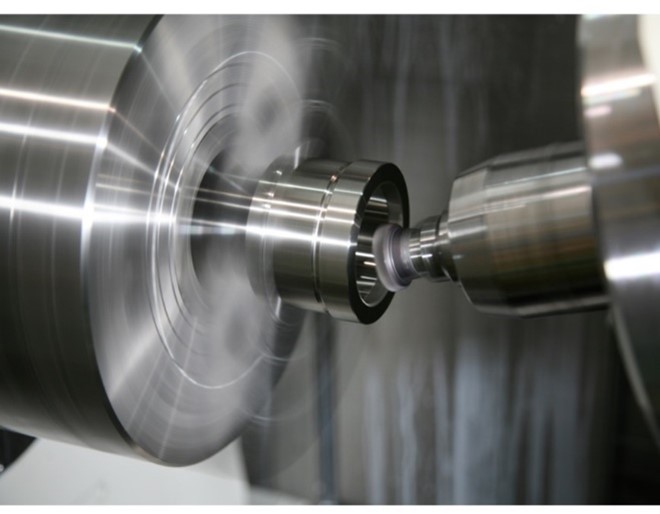
3-3. Gear Shaping
Gear shaping uses a special tool called a pinion cutter, which has a gear tooth profile. The process involves gradually cutting as the tool moves back and forth. This method is suitable for both external and internal gear machining, and even when there are steps or interfering features, it allows for machining close to those areas.
While gear skiving can also reach near interfering features, it requires tilting the tool to accommodate the crossing angle. When you need to get even closer to the interference, gear shaping is the better choice.
On multitasking machines, similar operations can be performed using a pinion cutter. However, the back-and-forth motion of the cutter is less efficient than with dedicated machines, which means high-speed machining is not possible. Still, since there’s no need to invest in a dedicated machine, gear shaping on a multitasking machine can be a practical solution.
3-4. Gear Milling
Gear milling involves using a form cutter, where the teeth of a T-slot cutter are shaped into a gear profile. Since the gear grooves are processed one at a time, a high-precision indexing table is necessary.
Multitasking machines are equipped with a C-axis (angle indexing axis), allowing the indexing of gear grooves to be easily controlled by an NC program. Although processing each groove individually results in longer cycle times, gear milling can reach areas that would otherwise be inaccessible with a hob cutter due to interference.
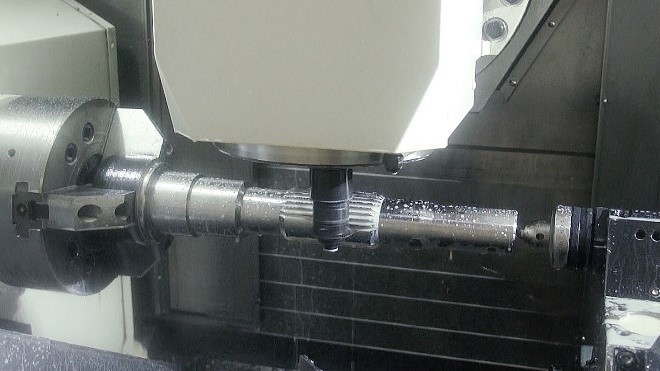
3-5. Gear Machining by Milling
Gear machining by milling involves cutting each tooth groove individually using tools such as end mills. This method does not require dedicated gear-cutting tools, allowing the use of general-purpose milling tools, which makes it especially suitable for prototyping and small-lot production.
Since multitasking machines can perform milling operations like machining centers, they allow gears to be machined using this method. However, when generating the machining program, CAM software is required.
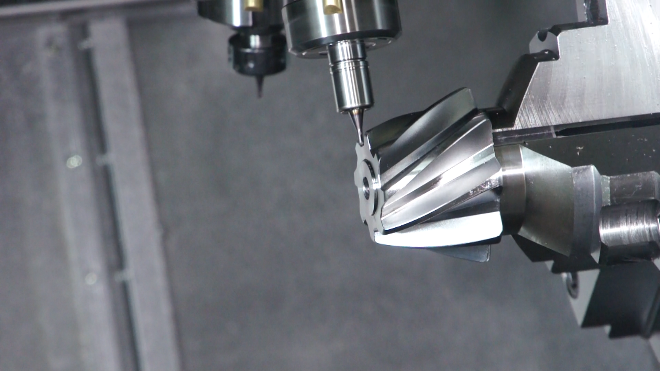
4. NC Options for Gear Cutting
When performing gear cutting on a multitasking machine, it is necessary to have a dedicated NC option for gear cutting. Using these specialized NC options, the spindle and cutter rotation axes can be synchronized. Below, we introduce two representative NC options: the electronic gearbox and flexible synchronization.
4-1. Electronic Gearbox
The electronic gearbox synchronizes by having the slave spindle follow the master spindle’s feedback. It continuously monitors (provides feedback) on the cutter’s rotation speed to control the work spindle, ensuring high-precision synchronization. However, this option cannot be used for high-speed machining, as it requires constant feedback during operation. Additionally, synchronization control is limited to the same system, so switching between the same tool spindle’s first and second operation spindles is not possible, meaning synchronization can only occur on one spindle at a time.
4-2. Flexible Synchronization
Flexible synchronization sends synchronization commands and feedback to both the master and slave spindles from the NC. Unlike the electronic gearbox, flexible synchronization allows for control at high rotational speeds and the ability to switch synchronization control between different systems. This makes it ideal for gear skiving operations. When machining gears across multiple stages, or when gear cutting occurs in several areas, flexible synchronization control is the preferred choice.
5. Conclusion
In this article, we introduced various gear machining methods using multitasking machines. Gear cutting techniques, such as hobbing, gear skiving, and gear milling, cover a wide range of possibilities. By selecting the most suitable method based on the gear shape to be processed, you can achieve efficient and effective machining.
Nakamura-Tome Products and Gear Machining
When Nakamura-Tome’s multitasking machines are equipped with the gear cutting option, they come with a standard module for generating hobbing programs. By simply inputting specifications in a dialogue format, the NC program is automatically created, taking hob shifts into account, making it easy for even beginners to generate gear machining programs.
Additionally, if the flexible synchronization option is installed, a module for generating gear skiving programs is also included as a standard feature.
[Programming Support Software]
The NC programming support software, “Smart Support,” helps you easily create hobbing and gear skiving programs. Processes using original Nakamura-Tome G codes are pre-registered as fixed templates, allowing users to generate programs simply by entering parameters while referring to 3D on-screen guidance images and instructional prompts.
Smart Support is integrated into the NT SmartX control system.
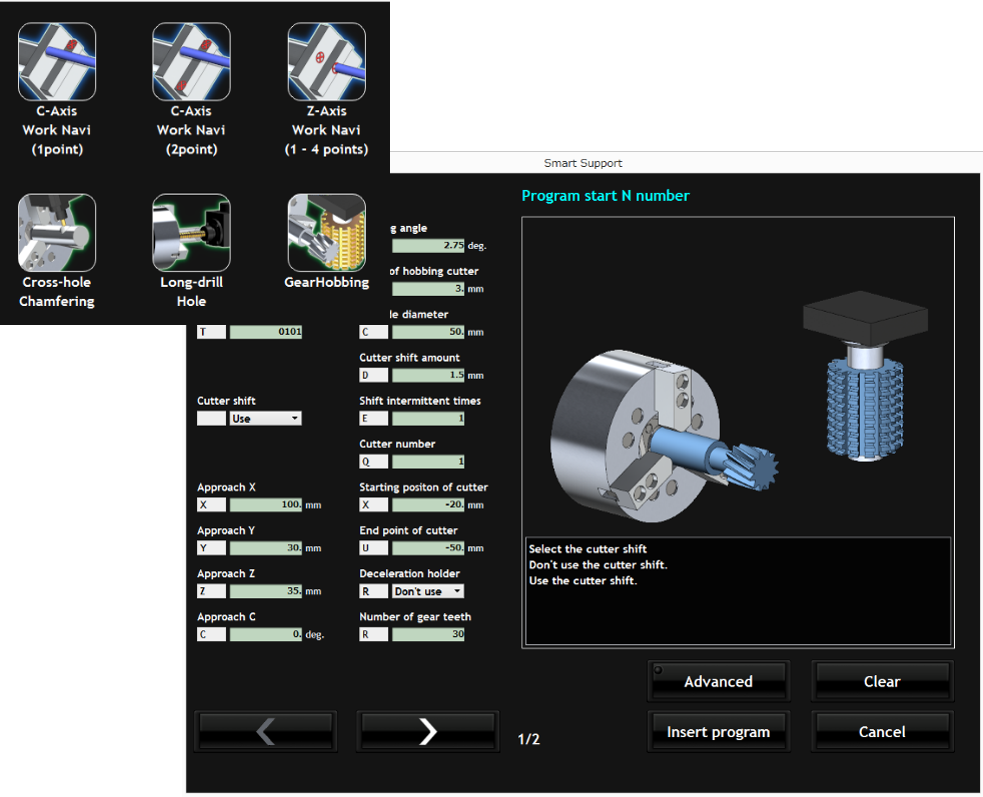