Medical
Shoulder Implant
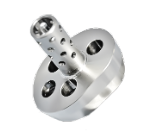
- Titanium Ti-6AI-4V
Metal Head
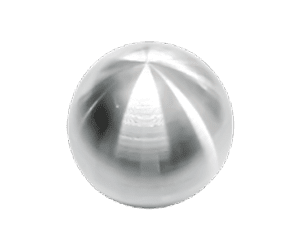
- φ28 CoCrMo
Femur Support
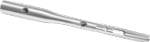
- φ22×220L
Hip Cup
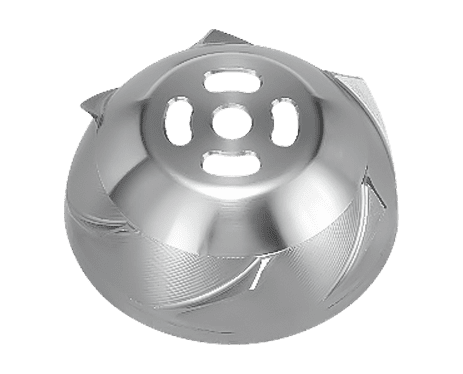
- φ45 Bar material β-Titanium
Artificial Knee Joint
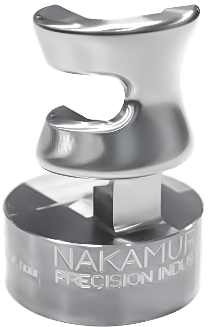
- φ70×100L Titanium Ti-6AI-4V(Grade 5)
Microscope Part
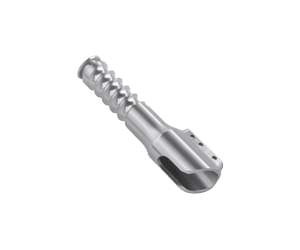
- φ30 Bar material SUS303
Artificial Heart Pump
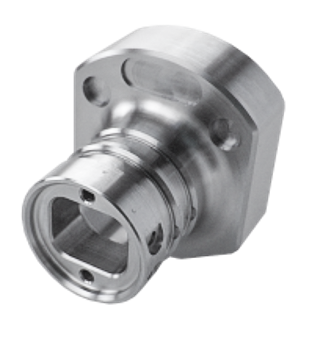
- φ40×500L β-Titanium
Endoscope
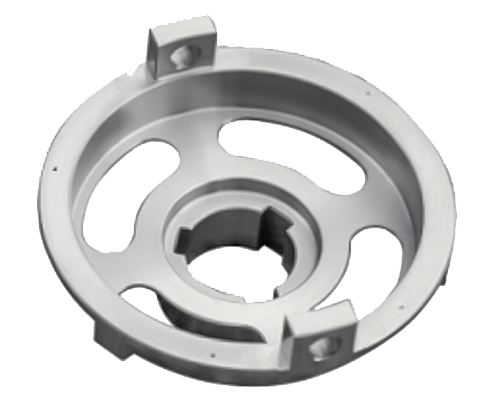
- φ65 Bar material SUS303
Bone Screw
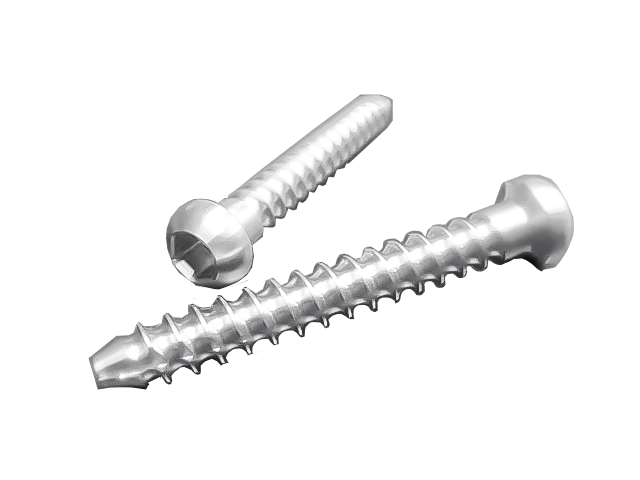
- φ23
Intramedullary Rod
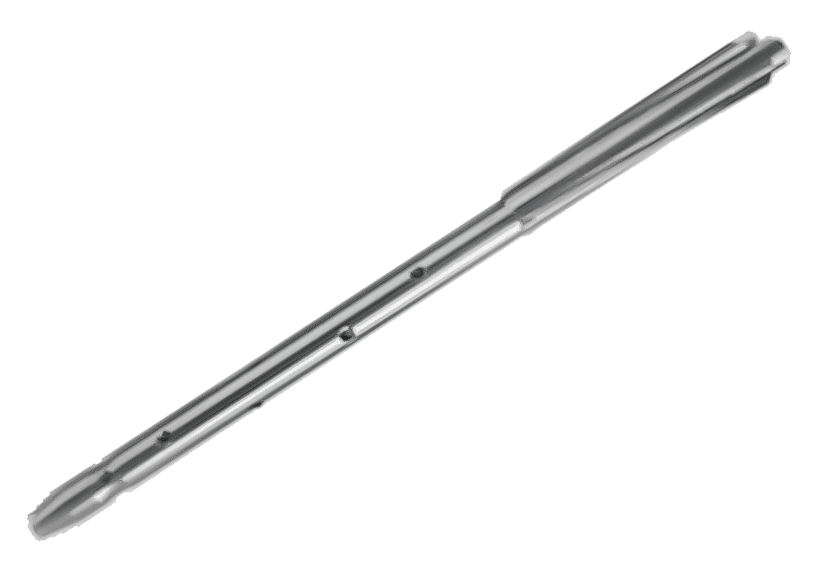
- φ16
Connector
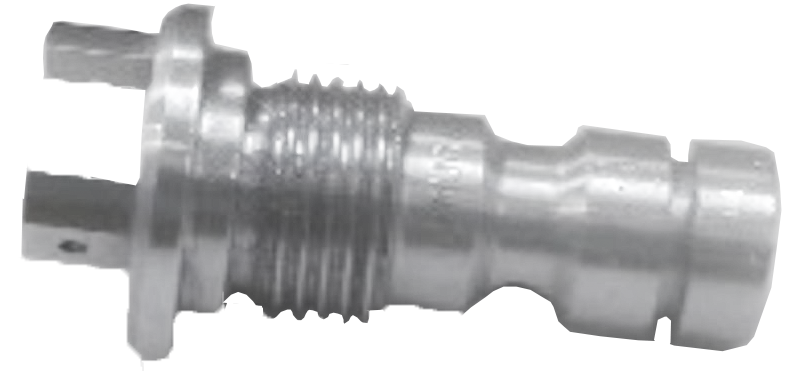
- φ25×50L SUS303
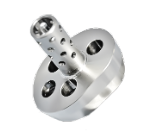
Material | Titanium Ti-6AI-4V |
Point In the mass production of medical components, high-efficiency angled hole machining using a B-axis turret has been achieved.
Click to play video
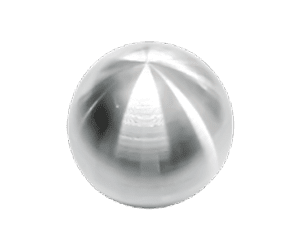
Diameter | φ28 |
Material | CoCrMo |
Point High-precision machining has been achieved, successfully controlling sphericity to within 5μm and surface roughness (Ra) to approximately 0.2μm in continuous machining.
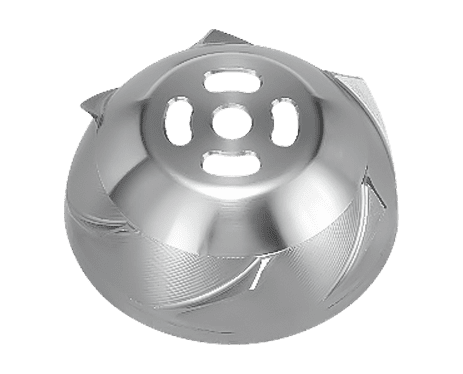
Diameter | φ45 |
Material | Bar material β-Titanium |
Point Complete processing from bar material to finished product can be done with a single machine.
Click to play video
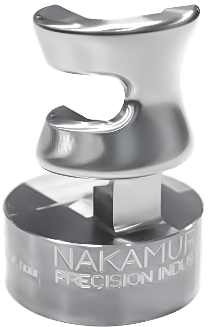
Diameter | φ70×100L |
Material | Titanium Ti-6AI-4V(Grade 5) |
Point The milling of knee joints and the customization of shapes to fit patients have been achieved through CAM software.
Click to play video
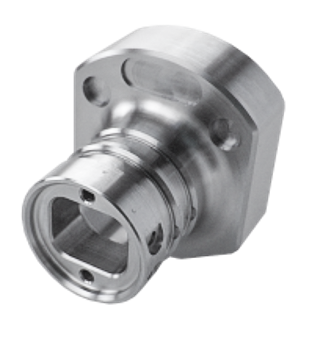
Diameter | φ40×500L |
Material | β-Titanium |
Point By having the three turrets perform simultaneous machining operations, high-efficiency processing has been achieved, resulting in significant cycle time reduction. This has enabled production from bar material to finished products.
Click to play video